What is Electrical Testing & Tagging?
Electrical Testing & Tagging in the workplace is a critical process that involves inspecting electrical equipment to ensure it’s safe for use. This process includes checking for any potential electrical faults, wear, or damage and tagging each piece of equipment as a record of its inspection status.
In New Zealand, electrical testing & tagging aligns with the Health and Safety at Work Act 2015, which mandates that employers provide a safe work environment, including safe equipment and machinery. Ensuring electrical equipment is properly tested helps reduce the risk of electrical hazards, such as shocks or fires, which can cause injuries or even fatalities.
Electrical testing & tagging involves specialised tester to measure the integrity of cables, insulation, and earth connections, then marking each item with a tag indicating the test date, results, and the next due date for testing. By regularly testing and tagging, workplaces can proactively identify potential issues, maintain compliance with safety regulations, and foster a safer work environment for everyone.
Electrical Testing & Tagging
We offer electrical testing & tagging of all portable appliances (PAT), and includes testing of 3-phase equipment.
We are fully mobile and can come to your site, with the latest equipment to make the testing efficient and as least disruptive as possible. No job too big or small- we offer a unique approach to our testing that will save you money!
We also offer special pricing in January and February to students attending University Halls of Residence or Boarding School, who require their electrical items tested and tagged.
Contact us for further information and pricing.
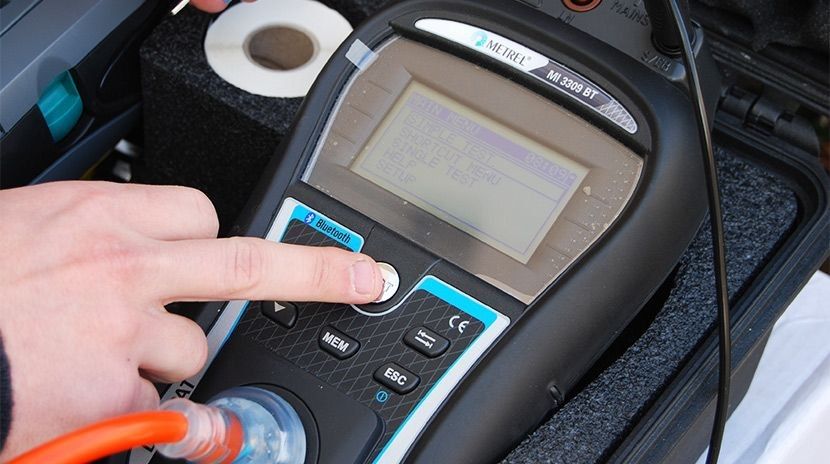